Ключевым фактором их эффективности является не только программное обеспечение и электроника, но и конструкция корпуса. В этом контексте технологии лазерной резки открывают новые горизонты для создания легких, прочных и аэродинамически оптимизированных корпусов для БПЛА.
Метод лазерной резки обладает рядом преимуществ, которые делают его идеальным для создания сложных и точных деталей, необходимых для эффективной работы БПЛА. Рассмотрим ключевые аспекты применения лазерной резки в этой области.
▎Преимущества лазерной резки в производстве БПЛА:
Лазерная резка — это высокоточная технология, позволяющая создавать детали любой сложности с минимальными затратами времени и материалов. Она обеспечивает:
1. Высокая точность и качество:
• Высокая точность: Лазерная резка обеспечивает высокую степень точности, что критично для деталей БПЛА, где даже небольшие отклонения могут повлиять на аэродинамические характеристики.
• Чистота реза: Лазерный процесс оставляет минимальные следы и не требует дополнительной обработки краев, что сокращает время производства.
2. Скорость производства:
• Быстрая обработка: Лазерные машины могут обрабатывать материалы быстрее, чем традиционные методы, что позволяет ускорить производственный процесс и сократить время выхода на рынок.
• Автоматизация: Современные лазерные системы могут быть интегрированы в автоматизированные производственные линии, что увеличивает эффективность.
3. Гибкость в дизайне:
• Сложные формы: Лазерная резка позволяет создавать детали с сложными геометрическими формами и узорами, что дает возможность разрабатывать уникальные конструкции БПЛА и открывает новые горизонты для дизайнеров и инженеров в разработке инновационных решений для БПЛА.
• Производство малых серий: Лазерная резка идеально подходит для прототипирования и производства малых серий, что позволяет быстро тестировать новые идеи и концепции.
4. Поддержка прототипирования: Наша технология позволяет быстро создавать прототипы, что упрощает процесс тестирования и доработки новых моделей БПЛА.
5. Разнообразие материалов:
• Широкий выбор: Лазерная резка может использоваться для различных материалов, включая алюминий, углеродные композиты, пластик и даже дерево, что делает ее универсальным инструментом для производства БПЛА.
• Легкость и прочность: Использование легких и прочных материалов снижает вес БПЛА и улучшает его летные характеристики.
6. Экономия затрат:
• Снижение отходов: Лазерная резка минимизирует отходы материала благодаря высокой точности реза, что снижает общие затраты на производство.
• Снижение трудозатрат: Автоматизация процесса уменьшает необходимость в ручном труде, что также способствует экономии.
▎Оптимизация аэродинамических свойств
Корпус БПЛА играет критическую роль в его аэродинамике. С помощью лазерной резки можно создавать формы, которые минимизируют сопротивление воздуха, увеличивая маневренность и скорость полета. Например, использование обтекаемых форм и интеграция элементов, улучшающих поток воздуха, могут существенно повысить общую эффективность беспилотника.
▎Выбор материалов
Для лазерной резки доступны различные материалы, каждый из которых обладает своими уникальными свойствами:
• Композитные материалы: Они легкие и прочные, что делает их идеальными для создания корпусов БПЛА. Композиты также обладают хорошими аэродинамическими характеристиками.
• Алюминий: Этот материал обеспечивает отличную прочность при низком весе. Алюминиевые корпуса могут быть использованы в более тяжелых БПЛА, где требуется высокая прочность.
• Пластики: Современные пластики, такие как ABS или поликарбонат, позволяют создавать легкие и устойчивые к воздействию внешней среды корпуса.
Каждый из этих материалов может быть обработан с помощью лазерной резки, что делает процесс производства более эффективным и экономичным.
▎Влияние на производительность БПЛА
Правильный выбор материала и конструкции корпуса напрямую влияет на производительность беспилотника. Легкие корпуса позволяют увеличить время полета и маневренность, в то время как прочные конструкции обеспечивают защиту внутренних компонентов от внешних воздействий. Кроме того, оптимизированные аэродинамические свойства способствуют снижению расхода энергии, что также положительно сказывается на общем времени работы БПЛА.
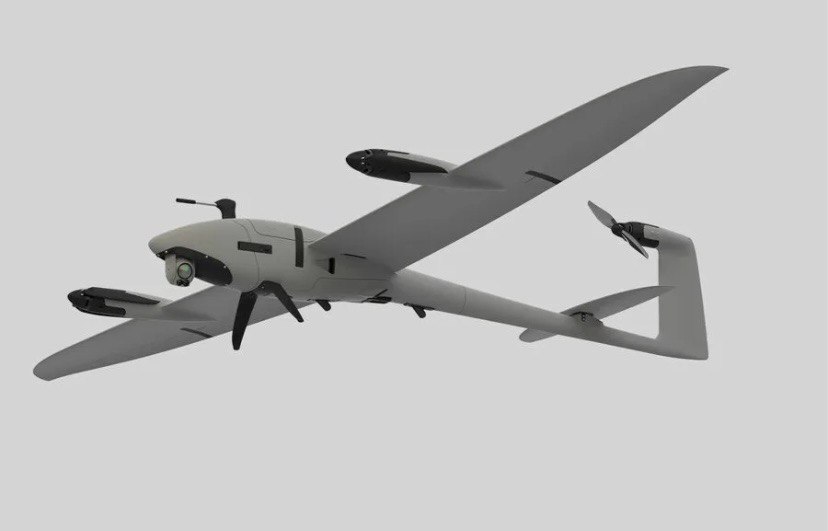
Подробнее посмотреть наши работы вы можете на странице фрезеровка и лазерная обработка изделий.
Что такое лазерная резка и как она применяется в производстве БПЛА?
Лазерная резка — это процесс, при котором мощный лазерный луч используется для точного и чистого разрезания различных материалов, таких как металл, пластик, дерево и композитные материалы. Эта технология обеспечивает высокую степень точности, минимальные отходы и возможность создания сложных форм, что делает ее идеальным решением для производства деталей БПЛА.
▎Применение лазерной резки в производстве БПЛА
Лазерная резка находит широкое применение в различных аспектах производства БПЛА:
• Изготовление каркасов: Легкие и прочные каркасные конструкции могут быть созданы с помощью лазерной резки, что способствует улучшению аэродинамических характеристик и общей эффективности аппарата.
• Производство элементов управления: Точные детали для систем управления и навигации БПЛА могут быть изготовлены с высокой степенью точности, что гарантирует надежность работы всех механизмов.
• Создание корпуса, обшивки и других компонентов: Лазерная резка используется для создания корпусов БПЛА, которые требуют точности и легкости. Лазерная резка позволяет быстро и точно изготавливать обшивку и другие внешние элементы БПЛА, что улучшает его внешний вид и функциональность.
• Крепежные элементы: Создание крепежных деталей и элементов соединения, которые обеспечивают надежность конструкции.
Лазерная резка является неотъемлемой частью современного производства БПЛА, обеспечивая высокую точность, скорость и гибкость в создании сложных деталей. Рекламно-производственная компания, занимающаяся лазерной резкой, может предложить своим клиентам широкий спектр услуг по созданию индивидуальных решений для их проектов в области беспилотных летательных аппаратов. Обращаясь к таким компаниям, производители БПЛА получают доступ к передовым технологиям и могут значительно повысить конкурентоспособность своей продукции.
Как быстро можно изготовить корпус для БПЛА с помощью лазерной резки?
Скорость изготовления корпуса для БПЛА с помощью лазерной резки зависит от нескольких факторов, включая:
1. Сложность дизайна: Более сложные и детализированные конструкции требуют больше времени для обработки. Простые формы могут быть вырезаны быстрее.
2. Размер корпуса: Большие детали займут больше времени на резку, чем маленькие.
3. Материал: Разные материалы имеют различные характеристики резки. Например, алюминий может резаться быстрее, чем сталь, но требует настройки оборудования.
4. Объем заказа: При массовом производстве время на подготовку и настройку оборудования может быть компенсировано за счет скорости серийного производства.
5. Подготовка файлов: Время, необходимое для подготовки CAD-файлов и настройки лазера, также влияет на общую скорость изготовления.
В общем случае, для простых корпусов из легких материалов (например, акрил или фанера) можно ожидать, что процесс займет от нескольких часов до одного-двух дней, включая время на подготовку и финальную обработку. Для более сложных или больших деталей это может занять несколько дней.
Если у вас есть конкретный проект, лучше всего обратиться к производителю для получения оценки времени на основе ваших требований.
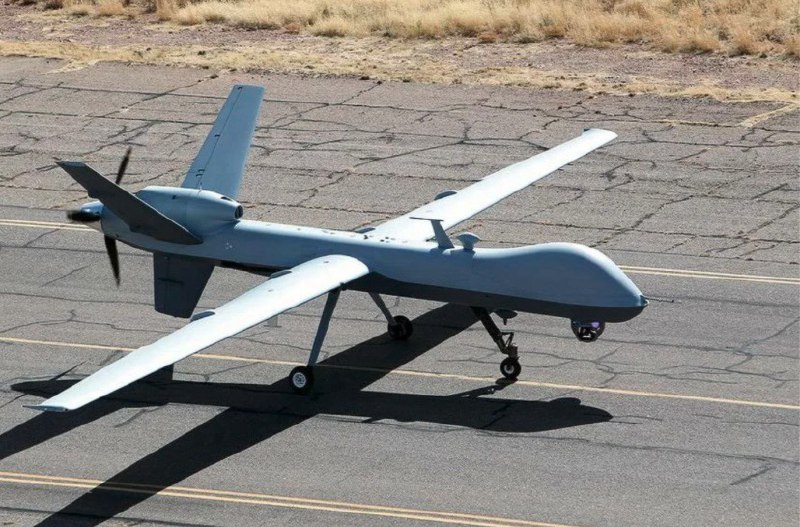
Подробнее ознакомиться с информацией вы можете на странице фрезеровка и лазерная обработка изделий.
Как лазерная резка влияет на аэродинамические свойства корпуса БПЛА?
Лазерная резка может оказывать как положительное, так и отрицательное влияние на аэродинамические свойства корпуса БПЛА (беспилотного летательного аппарата). Вот несколько ключевых аспектов:
▎Положительное влияние:
1. Точная геометрия: Лазерная резка обеспечивает высокую точность и чистоту краев, что позволяет создавать гладкие поверхности. Это может способствовать снижению сопротивления воздуха и улучшению аэродинамических характеристик.
2. Сложные формы: Лазерная резка позволяет создавать сложные геометрические формы, которые могут быть оптимизированы для аэродинамики. Например, можно реализовать обтекаемые профили, что также способствует улучшению аэродинамических свойств.
3. Легкость конструкции: Лазерная резка позволяет использовать легкие материалы, что снижает общий вес БПЛА и может улучшить его маневренность и эффективность.
▎Отрицательное влияние:
1. Качество краев: Если края не обработаны должным образом после лазерной резки, это может привести к образованию заусенцев или неровностей, что увеличивает сопротивление воздуха и ухудшает аэродинамику.
2. Тепловое воздействие: При лазерной резке может происходить термическое воздействие на материал, что иногда приводит к деформации или изменению свойств материала в зоне реза. Это может повлиять на прочность и стабильность конструкции.
3. Отсутствие тестирования: Если аэродинамические свойства корпуса не тестируются после его создания, то возможно, что оптимизация форм не будет достигнута, и это может привести к ухудшению летных характеристик.
В целом, лазерная резка может значительно улучшить аэродинамические свойства корпуса БПЛА, если процесс будет выполнен с учетом всех нюансов проектирования и обработки. Важно также проводить тестирование и анализ аэродинамических характеристик после изготовления для достижения наилучших результатов.
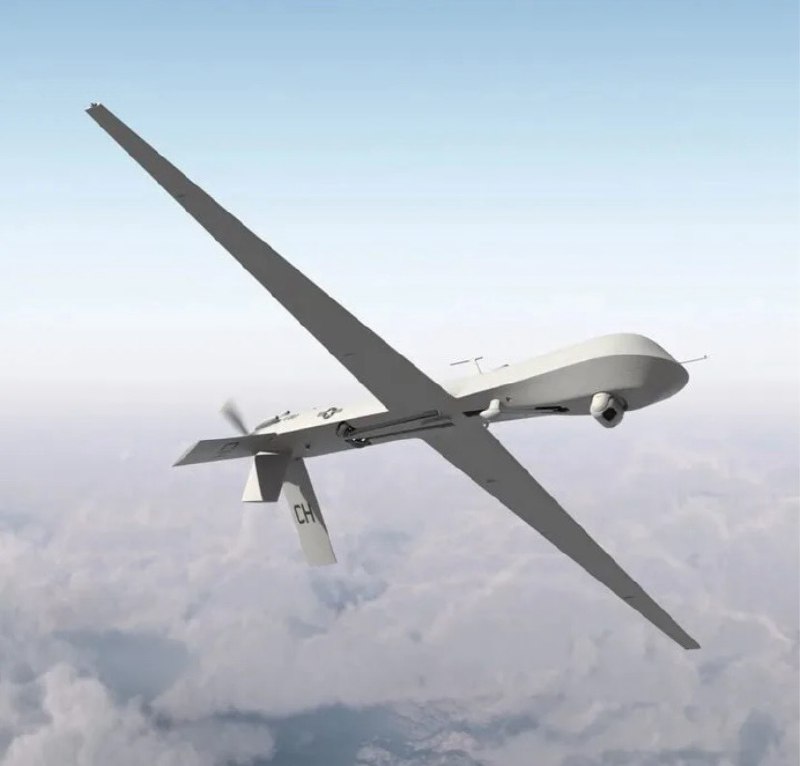
Подробнее посмотреть информацию вы можете на странице фрезеровка и лазерная обработка изделий.
Какие материалы подходят для лазерной резки при производстве корпусов БПЛА?
При производстве корпусов БПЛА для лазерной резки подходят различные материалы, в зависимости от требований к весу, прочности, аэродинамике и стоимости. Вот некоторые из наиболее распространенных материалов:
▎1. Пластики
• Акрил (PMMA): Легкий, прозрачный и прочный материал, который хорошо подходит для создания обтекаемых форм.
• Полиэтилен (PE): Устойчивый к ударам и химическим воздействиям, часто используется для создания легких конструкций.
• ПВХ: Доступный и легкий материал, который хорошо поддается лазерной резке.
• Полистирол (PS): Легкий и недорогой материал, который можно использовать для создания различных форм.
▎2. Композитные материалы
• Углеродные волокна: Обладают высокой прочностью при низком весе, идеально подходят для высокопроизводительных БПЛА.
• Стекловолокно: Также легкий и прочный материал, который часто используется в аэрокосмической отрасли.
▎3. Металлы
• Алюминий: Легкий и прочный металл, который хорошо подходит для лазерной резки. Используется в более тяжелых и мощных БПЛА.
• Нержавеющая сталь: Обладает высокой прочностью и коррозионной стойкостью, но требует более мощного лазера для резки.
• Латунь и медь: Могут быть использованы для специфических применений, хотя их резка может быть сложнее.
▎4. Дерево
• Фанера: Легкая и доступная, легко обрабатывается лазером. Подходит для прототипов и менее требовательных приложений.
• МДФ: Плотный древесно-волокнистый материал, который также хорошо поддается лазерной резке.
▎5. Тканевые материалы
• Нейлон и полиэстер: Используются для создания оболочек и других компонентов БПЛА, особенно в легких моделях.
Выбор материала зависит от конкретных требований к БПЛА, включая его назначение, условия эксплуатации и бюджет. Лазерная резка позволяет эффективно обрабатывать множество материалов, что делает ее популярным выбором в производстве корпусов БПЛА.
Как выбор материала влияет на производительность БПЛА?
Выбор материала для корпуса БПЛА (беспилотного летательного аппарата) существенно влияет на его производительность, включая такие аспекты, как вес, прочность, аэродинамика, стоимость и долговечность. Вот основные факторы, которые необходимо учитывать:
▎1. Вес
• Легкие материалы (например, углеродные волокна или акрил) позволяют снизить общий вес БПЛА, что может увеличить его маневренность и время полета. Легкие конструкции требуют меньшей мощности для подъема, что также снижает расход энергии.
• Тяжелые материалы (например, металл) могут увеличить вес и уменьшить время полета, но могут быть необходимы для обеспечения прочности в условиях высокой нагрузки.
▎2. Прочность и жесткость
• Прочные материалы (например, углеродные волокна или алюминий) могут выдерживать большие нагрузки и удары, что особенно важно для БПЛА, работающих в сложных условиях или при выполнении сложных маневров.
• Хрупкие материалы (например, акрил) могут быть менее устойчивыми к повреждениям, что может ограничить их применение в условиях высокой нагрузки.
▎3. Аэродинамика
• Гладкие и обтекаемые формы, созданные из материалов, которые легко обрабатываются (например, пластики), могут снизить сопротивление воздуха и улучшить эффективность полета.
• Неправильный выбор материала может привести к увеличению сопротивления воздуха, что негативно скажется на скорости и маневренности.
▎4. Стоимость
• Доступные материалы (например, фанера или ПВХ) могут снизить общую стоимость производства БПЛА, но могут потребовать компромиссов в отношении прочности и долговечности.
• Дорогие композитные материалы (например, углеродные волокна) могут повысить стоимость, но обеспечивают лучшую производительность и долговечность.
▎5. Температурные условия и устойчивость к внешним факторам
• Некоторые материалы могут быть более устойчивыми к воздействию влаги, солнечного света и температурных изменений. Например, композитные материалы часто обладают высокой коррозионной стойкостью.
• Неподходящие материалы могут привести к быстрому износу или повреждению БПЛА при эксплуатации в неблагоприятных условиях.
▎6. Энергетическая эффективность
• Легкие и прочные материалы могут улучшить энергетическую эффективность БПЛА, позволяя ему летать дольше на одном заряде аккумулятора.
Правильный выбор материала для корпуса БПЛА является критически важным для достижения оптимальной производительности. Он должен соответствовать требованиям к весу, прочности, аэродинамике и стоимости, а также учитывать условия эксплуатации. Каждый проект требует индивидуального подхода к выбору материалов для достижения наилучших результатов.
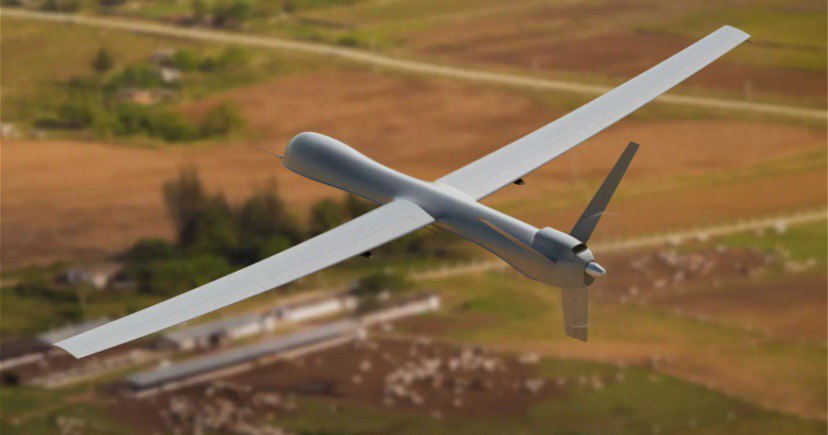
Подробнее ознакомиться с информацией о ценах и сроках на странице фрезеровка и лазерная обработка изделий.
Можно ли мы внести изменения в проект по лазерной резке для БПЛА во время процесса производства?
Внесение изменений в проект по лазерной резке для БПЛА во время процесса производства возможно, но этот процесс может быть сложным и требует внимательного подхода. Вот несколько факторов, которые следует учитывать:
▎1. Этап производства
• Если вы находитесь на ранних этапах производства, внесение изменений может быть проще и менее затратным. Например, если детали еще не были вырезаны, изменения в проекте могут быть реализованы без значительных последствий.
• Если детали уже вырезаны или находятся на финальных стадиях сборки, внесение изменений может потребовать переработки уже изготовленных компонентов, что увеличит время и затраты.
▎2. Техническая возможность
• Убедитесь, что оборудование для лазерной резки поддерживает необходимые изменения. Некоторые изменения могут требовать дополнительных настроек или даже другого оборудования.
• Также важно проверить, не повлияют ли изменения на другие компоненты или системы БПЛА.
▎3. Время и стоимость
• Внесение изменений может привести к задержкам в производственном процессе. Оцените, насколько критично это для вашего проекта.
• Изменения могут увеличить общую стоимость проекта из-за дополнительных затрат на материалы и трудозатраты.
▎4. Координация с командой
• Важно обеспечить хорошую коммуникацию между всеми членами команды, чтобы изменения были четко поняты и правильно реализованы.
• Если изменения затрагивают конструкцию или функциональность БПЛА, необходимо провести дополнительные обсуждения и согласования.
▎5. Тестирование и проверка
• После внесения изменений потребуется провести тестирование новых компонентов, чтобы убедиться, что они соответствуют требованиям по производительности и безопасности.
Внесение изменений в проект по лазерной резке БПЛА во время производства возможно, но требует внимательного планирования и оценки всех последствий. Лучше всего заранее определить возможные изменения и их влияние на процесс производства, чтобы минимизировать риски и затраты.
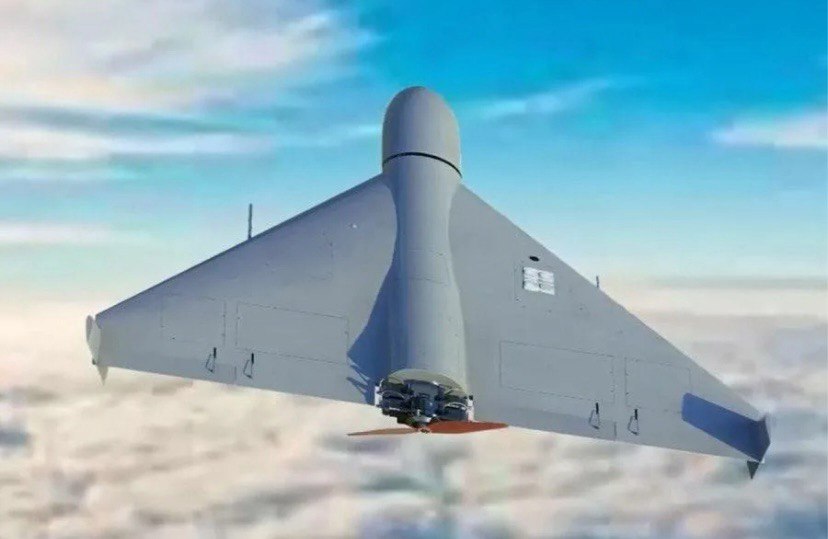
Подробнее о ценах и сроках на странице фрезеровка и лазерная обработка изделий.
Какова стоимость услуг лазерной резки для производства корпусов БПЛА?
Стоимость услуг лазерной резки для производства корпусов БПЛА может варьироваться в зависимости от нескольких факторов:
▎1. Материал
• Разные материалы (алюминий, сталь, композиты, пластик и т.д.) имеют разные стоимости обработки. Например, алюминий может быть дороже в обработке, чем пластик.
▎2. Толщина материала
• Чем толще материал, тем больше времени и энергии потребуется для его резки, что увеличивает стоимость.
▎3. Сложность дизайна
• Сложные детали с intricate (замысловатыми) формами требуют больше времени на программирование и резку, что также увеличивает стоимость.
▎4. Объем заказа
• Большие объемы заказов могут привести к снижению цены за единицу из-за экономии на масштабе.
▎5. Локация и оборудование
• Цены на услуги лазерной резки могут различаться в зависимости от региона и компании, предоставляющей услуги. Некоторые компании могут иметь более современное оборудование, что также может влиять на стоимость.
▎Дополнительные расходы
• Не забудьте учесть дополнительные расходы на:
• Подготовку файлов для резки.
• Обработку краев (если необходимо).
• Доставку и сборку готовых деталей.
▎Рекомендации
Для получения точной оценки рекомендуется обратиться к нескольким компаниям, предоставляющим услуги лазерной резки, с конкретными требованиями вашего проекта. Это поможет вам получить более точные расценки и выбрать наиболее подходящий вариант.
Как вы обеспечиваете качество продукции при лазерной резке?
Мы используем современное оборудование и технологии, а также проводим строгий контроль качества на всех этапах производства, чтобы гарантировать высокую точность и соответствие требованиям клиентов.
Заключение
Лазерная резка открывает новые возможности для разработки идеальных корпусов для беспилотников. Благодаря высокой точности, минимальным потерям материала и гибкости в дизайне, эта технология становится незаменимым инструментом для производителей БПЛА.
Выбор правильных материалов и применение инновационных подходов к дизайну помогут создать высокоэффективные беспилотные летательные аппараты, способные удовлетворить требования самых различных отраслей.
Если вы хотите узнать больше о возможностях лазерной резки 👀☝️для создания корпусов БПЛА или обсудить ваш проект, свяжитесь с нами!
Наша команда профессионалов "Центр Любой Резки №1"🏃♀️➡️🏃♂️➡️🏃➡️готова помочь вам реализовать ваши идеи с помощью передовых технологий.🤝
Как можно связаться с нами для обсуждения проекта по лазерной резке для БПЛА?
- Через наш сайт lyub-rezka.ru
- По телефону +7(952) 094-59-36
- По электронной почте lyubaya-rezka@yandex.ru
Наши менеджеры помогут вам обсудить детали и подготовить индивидуальное предложение.
Если у вас есть дополнительные вопросы, не стесняйтесь обращаться к нам! Мы всегда рады помочь вам сделать ваш проект уникальным, запоминающимся и реализовать ваши идеи!😊🙌